International Standards covering environmental management are intended to provide organizations with the elements of an effective environmental management system (EMS) that can be integrated with other management requirements and systems and help organizations achieve environmental and economic goals. The basis of the approach is shown in figure 2. The success of the system depends on commitment from all levels and functions of the organization, and especially from top management.
Progressive Stability in the Sustainability Context
Elasticity of management, entrepreneurship adaptability and stability are closely interconnected concepts. Elasticity of management is described in literature in four dimensions as: (1) reactive, (2) adaptive, (3) defensive and (4) creative attributes of the strategy of an observed firm (Å ebestová, 2012). Elasticity of enterprise management, as ability to react adequately at emerging conditions, is reflection and root of adaptability as enterprise’s ability to survive consistently changing conditions. Progressive stability is understood as adaptability so strong, that it enables enterprise to not only survive but continuously improve processes, become more robust and achieve better sustainable results that can be observed on selected criteria. Kovaľová concludes that entrepreneurship performance and effectiveness is directly connected with establishing its sustainable competitiveness (Kovaľová, 2011).
Sustainability concept with the accent on small and medium businesses (SMEs) should be examined in five important aspects (Scott, 2010; Pawliczek, 2011):
– Economic aspects (E)
– Social aspect (S)
– Environmental aspect (N)
– Technological aspect (T)
– Legislative and political (L).
A Polish research of SME de-conjuncture in the period 2007-2010 has discovered these important negative symptoms: (1) fall of sales and turnover, (2) fall of profit, (3) rise of operational costs, (4) rise of mistrust, (5) rise of employees’ fear of future, and more (Zakrzewska-Bielawska, 2011). Similar crisis/recession effect is expected to be apparent in enterprises in both Czech and Slovak Republics. Kočišová presents 2005/2006 indices of Slovak SMEs (value from interval -12 to 12 points): (1) average profit: value 7, (2) average turnover: value 11, (3) average number of employees: value -7, (4) investments into innovations: value -6 (Kočišová, 2010).
This paper addresses the following issues, each characterizing one or more aforementioned sustainability aspects (most close aspects):
– Trend of development of financial indicators: turnover, cost and profit of business (E);
– Investments and business development activity (E, T, N)
– Key customers and negotiated contracts (E, S)
– Trend of development of employment and employees´ affiliations (S, E)
– Trend of development of employees benefits (S)
– Satisfaction of employees and its measurement (S, E)
– Energy consumption and energy saving arrangements (N, E, T, L)
– Application of renewable energy sources RES (N, T, E, L)
– Separation and recycling of business waste (N, T, L)
– Usage of recycled materials and material saving arrangements (N, T, E, L).
On the basis of examined sustainability issues, these hypotheses were formulated:
HYP1: Application of ISO 9000 management system has positive effect on stability of business in the sustainability context on the basis of selected criteria.
HYP2: Application of ISO 14000 management system has positive effect on stability of business in the sustainability context on the basis of selected criteria.
HYP3: Application of ISO 9000 and ISO 14000 management systems has synergetic positive effect on stability of business in the sustainability context on the basis of selected criteria.
The validity of each hypothesis will be examined by analytical evaluation of leading questions/ criteria.
Original Research on Entrepreneurship Adaptability and its Methodology
The method used during the creation of this paper is described in this chapter. After preliminary research and inspiration from relevant scientific literature the researchers formulated the hypothesis. The hypothesis was subsequently evaluated by data analysis of questionnaire research characterized below.
Questionnaire Research
The questionnaire research was realized during the Spring semester 2012 by students of Business Entrepreneurship Faculty in Karvina, Silesian University in Opava (Czech Republic). 722 companies active in Czech and Slovak Republics in the period 2009-2011 were subjects of interest (SMEs are creating 89% of sample group in accordance with number of employees’ criterion). The interview protocol includes student-controlled interview with enterprise owner, executive manager or top manager, so the collected data have the character of expert guess opinion. Company identification (10 questions) and identification of student and their opinion on questionnaire relevance (5 questions) made a necessary part of each form. Initial sample size, 722 companies, were filtered and reduced to 677 credible items. The questionnaire form also includes nondisclosure statement to provide protection of confidential data. Moreover, data was analyzed anonymously and published as only no-name data.
Data reliability is assured by (1) authorization (contact person, signature, stamp), (2) subjective student relevance evaluation, partially (3) internet verification and (4) statistical validity (standard deviation).
The questionnaire focused on seven areas of interest (23 of 51 questions evaluated):
– Enterprise´s strategic management (6 questions)
– Economic and financial trends of business, risk management (5 of 11 questions evaluated),
– Personal politics of company (4 of 7 questions evaluated)
– Production, services and innovations (8 questions)
– Grants and subsidies (4 questions)
– Energetic and material savings and application of renewable sources (7 of 8 questions evaluated)
– Sustainability priorities of enterprises (7 of 7 questions evaluated).
Selected and Evaluated Questions (Criteria)
The following questions/criteria were evaluated. Numbering of questions correspond to that used in the questionnaire. Each part had enough space to comment on the questions and add further narrative information.
– Economic and financial trends of business (part C):
C1: How period 2009-2011 influenced business turnover?
C2: How period 2009-2011 influenced business costs?
C3: How period 2009-2011 influenced business profit?
C4: How period 2009-2011 influenced business assets (investments)?
C6: How long in advance company usually arranges contracts?
– Personal politics of company (part D):
D3: How period 2009-2011 influenced number of employees?
D2: How period 2009-2011 influenced present employee affiliations?
D1: How period 2009-2011 influenced employee benefits?
D9: Has the company researched or measured employees’ satisfaction?
– Energetic and material savings and application of renewable sources (part G):
G7: How period 2009-2011 influenced energy consumption?
G2: Have you realized arrangements for energy savings?
G9: What percentage of needed energy do you obtain from RES?
G3: What kind of RES do you apply? — complementary question
G8: Have you realized arrangements for material savings?
G4: Do you separate and recycle business waste?
G10: How many of material inputs is recycled material? — complementary question
Data Analysis
For the sake of comparison, data was structured into four data evaluation groups:
– Enterprises with neither ISO 9000 nor ISO 14000 implemented — expected to be less stable (414 enterprises).
– Enterprises with ISO 9000 implemented (249 enterprises). 42% of companies with ISO 9000 have also ISO 14000.
– Enterprises with ISO 14000 implemented (121 enterprises). 88% of companies with ISO 14000 have also ISO 9000.
– Enterprises with both ISO 9000 and ISO 14000 implemented — expected to be the most stable and synergic (107 enterprises).
Data were processed by Microsoft® Excel. Tables and charts are presented and commented on in the next chapter. Discussion with other published related scientific results is presented later.
Findings and Results
The following paragraphs and figures describe research results concerning impact of ISO 9000 and/or ISO 14000 on selected criteria using minima-maxima differential analysis comparing group of interest with worst performance (usually without implemented ISO QMS) to group of interest with best performance. The “all data” group is presented as average value to show well apparent difference between “no ISO” group and ISO implemented groups’ performance.
ISO 9000 and 14000 Management Systems and Enterprise Financial and Business Trends
Five criteria concerning financial and business trends of enterprises are evaluated below.
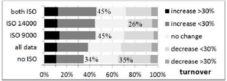
Figure 3. Evaluation of the Criterion C1 — How Period 2009-2011 Influenced Business Turnover?
45% of enterprises which implemented both ISO EMS or at least ISO 9000 indicated increase of turnover and only 34% of enterprises which did not implement any ISO EMS indicated increase of turnover, so the maximum-minimum difference is 11%. On the other side, only 26% of enterprises which did implement ISO 14000 indicated decrease of turnover with comparison to 35% which did not implement any ISO EMS and indicated decrease of turnover, so the maximum-minimum difference is 9%. Together, the highest positive ISO implementation effect on enterprises is 20% higher possibility of better turnover performance compared to ISO resistant companies.
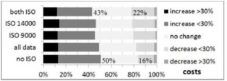
Figure 4. Evaluation of the Criterion C2 — How Period 2009-2011 Influenced Business Costs?
Only 43% of the enterprises which implemented both ISO EMS indicated increase of costs in comparison to 50% which did not implement any ISO EMS, indicating increase of costs, so the maximum-minimum difference is 7%. On the other side, 22% of the enterprises which implemented both ISO EMS indicated decrease of costs and only 16% enterprises which did not implement any ISO EMS declare decrease of costs, so the maximum-minimum difference is 6%. Altogether, the highest positive ISO implementation effect on enterprises is 13% higher possibility of better costs performance compared to ISO resistant companies.
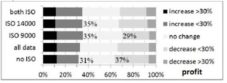
Figure 5.Evaluation of the Criterion C3 — How Period 2009-2011 Influenced Business Profit (EBIT)?
35% of the enterprises which implemented ISO 9000 or ISO 14000 EMS indicated increase of profit and only 31% which did not implement any ISO EMS indicated increase of profit, so the maximum-minimum difference is 4%. On the other side, only 29% which implemented ISO 9000 indicated decrease of profit with comparison to 37% which did not implement any ISO EMS and indicated decrease of profit, so the maximum-minimum difference is 8%. Altogether, the highest positive ISO implementation effect on enterprises is 12% higher possibility of better profit performance compared to ISO resistant companies.

Figure 6. Evaluation of the Criterion C4 — How Period 2009-2011 Influenced Business Assets (Investments)?
41% of the enterprises which implemented both ISO EMS or at least ISO 9000 indicated increase of assets and only 32% enterprises which did not implement any ISO EMS indicated increase of assets, so the maximum-minimum difference is 9%. On the other side, only 12% which implemented either both ISO EMS or at least ISO 14000 indicated decrease of assets with comparison to 17% which did not implement any ISO EMS and indicated decrease of assets, so the maximum-minimum difference is 5%. Together, the highest positive ISO implementation effect on enterprises is 14% higher possibility of better investment performance compared to ISO resistant companies.
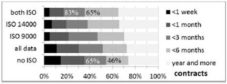
Figure 7. Evaluation of the Criterion C6 — How Long in Advance Company Usually Arranges Contracts?
The analysis is realized on two representative groups: (a) contracts arranged usually more than 1 month in advance and (b) 6 months in advance. 83% of the enterprises which implemented both ISO EMS indicated contacts arranged usually more than 1 month in advance and only 65% which did not implement any ISO EMS indicated contacts arranged usually more than 1 month in advance, so the maximum-minimum difference is18%. Also 65% which implemented both ISO EMS indicated contacts arranged usually more than 6 months in advance with comparison to 46% which did not implement any ISO EMS and indicated contacts arranged usually more than 6 months in advance, so the maximum-minimum difference is 19%. This criterion is most likely sensible on business branches and less applicable for some NACE branches such as for example catering services, which are characterized with fast reaction to customer demands, however this sensibility was not tested.
ISO 9000 and 14000 Management Systems and Sustainability Issues of Enterprise´s Personal Politics
Four criteria concerning personal politics are evaluated below.
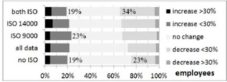
Figure 8. Evaluation of the Criterion D3 — How Period 2009-2011 Influenced Number of Employees?
23% of the enterprises that implemented ISO 9000 showed indicated an increase in the number of employees, and only 19% which did not implement ISO or EMS indicated an increased number of employees, the maximum-minimum difference is thus 4%. Surprisingly, a very low rate (19%) of enterprises which did implement both ISO and EMS had an increased number of employees too. On the other side, 34% of the enterprises which implemented both ISO and EMS indicated a decrease in the number of employees with comparison to 23% which did not implement ISO or EMS and indicated a fall in the number of employees, so the maximum-minimum difference is -11% (minus is placed, due to the fact that value is understood as negative, since the positive phenomenon is considered rise of employment). A similar trend shows also ISO 9000 or 14000 implemented separately. A summary observation is that the implementation of ISO (especially 14000 and both) has some negative effect on employees’ number, most likely due to carried cost optimization process.
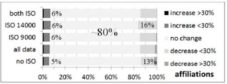
Figure 9. Evaluation of the Criterion D2 — How Period 2009-2011 Influenced Present Employee Affiliations?
6% of the enterprises which implemented ISO 9000 and/or ISO 14000 indicated increased affiliations of present employees, and only 5% which did not implement any ISO EMS indicated increased affiliations of present employees, so the maximum-minimum difference is 1%. On the other side, 16% of the enterprises which implemented ISO 14000 indicated decreased affiliations of present employees in comparison to 13% enterprises which did not implement any ISO EMS and indicated decreased affiliations of present employees, so the maximum-minimum difference is -3% (minus is placed, due to the fact that value is understood as negative, since the positive phenomenon is considered rise of affiliations). A similar but subtle trend shows also ISO 9000 and both ISO implemented data groups. It can be observed, that implementation of ISO (especially 14000) has either no or slightlynegative effect on present employees’ affiliations, most likely due to carried cost optimization process.
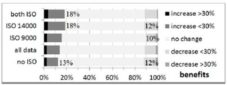
Figure 10. Evaluation of the Criterion D1 — How Period 2009-2011 Influenced Employee Benefits?
18% of the enterprises which did implement both ISO EMS or ISO 14000 indicated increase of employees benefits, and only 13% which did not implement any ISO EMS indicated increase of employees benefits, so the maximum-minimum difference is 5%. On the other hand, 12% of the enterprises which implemented ISO 14000 and those which did not implement any ISO EMS indicated decrease of employees benefits with comparison to10% enterprises which implemented ISO 9000 and indicated decrease of employees benefits, so the maximum-minimum difference is 2% This subtle positive trend shows also both ISO-implemented groups.
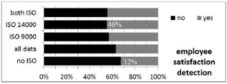
Figure 11. Evaluation of the Criterion D9 — Have the Company Researched or Measured Employees’ Satisfaction?
46% of the enterprises which implemented ISO 14000 realized measurement of employees’ satisfaction, and only 32% which did not implement ISO EMS realized measurement of employees’ satisfaction, so the maximum-minimum difference is14%. A similar positive trend shows also ISO 9000 and both ISO implemented data groups.
ISO 9000 and 14000 Management Systems and Sustainability Issues of Energetic and Material Savings and Application of Renewable Sources
Five criteria concerning issues of energetic and material savings and application of renewable sources are evaluated below.
Figure 12. Evaluation of the Criterion G7 — How Period 2009-2011 Influenced Energy Consumption?
As much as 36% of the enterprises which implemented ISO 9000 indicated increased energy consumption, and 32% which did implement both ISO EMS indicated increased energy consumption, so the maximum-minimum difference is 4%. A similar low rate (33%) of increased energy consumption indicated enterprises which did not implement any ISO EMS too. On the other hand, 14% of the enterprises which implemented either both ISO EMS or ISO 14000 indicated decreased energy consumption with comparison to 9% which did not implement any ISO EMS and indicated decreased energy consumption, so the maximum-minimum difference is 5%. A similar trend shows also ISO 9000 data group. A summary observation is that implementation of ISO 9000 has a slightly negative effect on energy consumption, and implementation of ISO 9000 or both ISO data group has a slightly positive effect on energy consumption.
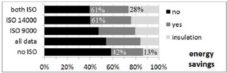
Figure 13. Evaluation of the Criterion G2 — Have You Realized Arrangements for Energy Savings?
61% of the enterprises which implemented either both ISO EMS or ISO 14000 realized arrangements for energy savings, and only 42% which did not implement any ISO EMS realized arrangements for energy savings, so the maximum-minimum difference is19%. Also 28% of the enterprises which implemented both ISO EMS made thermal insulations on their facilities with comparison to 13% enterprises which did not implement any ISO EMS and made thermal insulations on their facilities, so the maximum-minimum difference is 15%.
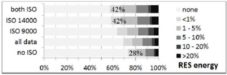
Figure 14. Evaluation of the Criterion G9 — What Percentage of Needed Energy Do You Obtain from RES?
42% of the enterprises which did implement either both ISO EMS or ISO 14000 obtain energy from RES and only 28% which did not implement any ISO EMS obtain energy from RES, so the maximum-minimum difference is 14%.Structure of RES applied by respondents (according to the complementary question G3: what kind of RES do you apply?) is as the following: (a) LPG: 10 — 12%, (b) solar heating: 8 — 10%, (c) photovoltaics: 3 — 5%, (d) other: 2 — 8%.
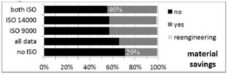
Figure 15. Evaluation of the Criterion G8 — Have You Realized Arrangements for Material Savings?
46% of the enterprises which implemented both ISO EMS realized arrangements for material savings and only 29% which did not implement any ISO EMS realized arrangements for material savings, so the maximum-minimum difference is17%. Reengineering of production realized circa 2% of companies that implemented ISO 14000.
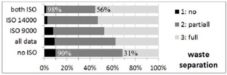
Figure 16. Evaluation of the Criterion G4 — Do You Separate and Recycle Business Waste?
98% of the enterprises which implemented both ISO EMS separate and recycle business waste partially and only 90% which did not implement any ISO EMS separate and recycle business waste partially, so the maximum-minimum difference is 8%. Also 56% of the enterprises which did implement both ISO EMS, separate and recycle business waste fully with comparison to 31% enterprises that did not implement any ISO EMS and separate and recycle business waste fully, so the maximum-minimum difference is 25%.Rate of respondents using recycled material (according to the complementary question G10: How many of material inputs are recycled material?) is as the following: (a) no ISO group: up to 68%, (b) ISO 9000 group: up to 72%, (c) ISO 14000 group: up to 78%, (d) both ISO groups: up to 76%. 43 — 47% of the enterprises use recycled material only up to 5% of their material needs.
Discussion
Validation or Dismissing of Hypotheses
Table 1 characterizes the possible percentage of improvement (change) of performance in criteria C1-G4 according to the comparison analysis results due to the implementation of ISO management systems. Percent values show how much more successful is a group of interest (ISO 9000, ISO 14000 and both ISO) than without ISO in selected criterion. The table is used to validate hypotheses.
Table 1. Hypotheses Validation Table
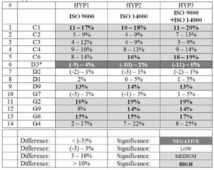
*Negative influence indicated
HYP1: 4 out of 14 criteria indicated high significance and 6 out of 14 criteria indicated medium significance (see table 1). Only 3 out of 14 criteria indicated low significance and one criterion indicated negative influence. Application of ISO 9000 management system has positive effect on stability of business in the sustainability context on the basis of selected criteria — hypothesis confirmed.
HYP2: 6 out of 14 criteria indicated high significance and 4 out of 14 criteria indicated medium significance (see Table 1). Only 3 out of 14 criteria indicated low significance and one criterion indicated negative influence. Application of ISO 14000 management system has positive effect on stability of business in the sustainability context on the basis of selected criteria — hypothesis confirmed.
HYP3: 6 out of 14 criteria indicated high significance and 4 out of 14 criteria indicated medium significance (see Table 1). Only 3 out of 14 criteria indicated low significance and one criterion indicated negative influence. Moreover, implementation of both ISO and QMS shows better performance in 7 criteria (C1, C2, C4, D1, G8 and G4), the same or very similar in 6 criteria (C3, D2, D9, G7, G2 and G9) and worse in 1 criterion (D3) than the implementation of ISO 9000 or ISO 14000 separately. Application of ISO 9000 and ISO 14000 management systems has synergetic positive effect on stability of business in the sustainability context on the basis of selected criteria — hypothesis confirmed.
Opinion of Other Related Research Studies
Kaynak explains that findings of his study, as well as of other research studies, support the positive effect of TQM practices on firms’ performance. A lack of top management commitment to the implementation of TQM has emerged as a possible reason for the failure of TQM systems in some organizations (Kaynak, 2003). In Samson’s opinion, three of the elements of TQM (leadership, people management and customer focus) have a significant positive effect on performance, but the other three categories (strategic quality planning, information and analysis and process management) do not (Samson, 1999). According to Mizla’s research of costs connected with quality, the highest operational profit reaches companies, which have higher fix costs on quality than variable costs on quality (Mizla, 2012). This indirectly impliesthat, companies which invested higher amount into quality prevention (QMS), do not have so high direct costs on quality (failures) and their economic performance is higher. Development of small- and medium-sized enterprises in Czech Republic requires investment in innovations and human resources’ development (Lundström, 2008). This statement resonates well with evaluated criteria C4 (investments), G2 (energy savings) and G8 (material savings). Němeček presented research results confirming, that added value, profit and work productivity are better when enterprises employ advanced technologies as TQM (ISO 9000), CNC, JIT, CRM and EAP (Němeček, 2011).
Koc pointed out that, findings of his research suggest a fit between ISO 9000 practices, manufacturing performance, competitive priorities and firm performance (Koc, 2007). Sharma concluded that the results of his study provide evidence that ISO 9000 certification is associated with improvements in financial performance especially in profit margin, growth of sales and earnings (Sharma, 2005).
The environment performance of SMEs and their long-term commitment to managing their environmental impacts must be increased and supported through simple, effective and strategic support systems (Burke, 2006). The study of Iraldo shows that, positive effect of well-implemented EMS on resource productivity, market performance and intangible assets is visible, however not strongly supported by statistical analysis. The EMSs in spite of their application in many years, have not yet achieved a high degree of “maturity” in their implementation (Iraldo, 2009). Numerous internal and external benefits are expected from the implementation of EMS. Communication channels, skills, knowledge and attitude are all improved in SMEs adopting EMS. EMS implementations open up new interactions between staff and management and provide intangible benefits like enhanced morale, which is deemed very important (Zorpas, 2010). Hillary concluded that extensive benefits accrue to SMEs adopting formal EMSs and this is widely reported in the analyzed studies. Disbenefits also exist, although there are less of them (Hillary, 2004). Ilomäki explains that the environmental management systems in Finland conditions are good tools for SMEs to reach their statutory requirements. However, EMSs do not appear to provide much impetus for SMEs to implement waste minimization (Ilomäki, 2001).
MacDonald discusses that corporations need a clear framework to effectively grapple with the challenge of moving toward a sustainable society. Furthermore, tools such as ISO 140001, while a useful start, do not in themselves assist an organization in strategic planning with true sustainability in mind (MacDonald, 2005). Gupta states that past research on sustainability has evaluated the role played by the approach of sustainability in driving green initiatives adopted by firm managers and the ability of opportunities created by the firm as a result of these initiatives to drive superior performance (Gupta, 2012). Sustainable management of all social, environmental and economic aspects within a company is increasingly becoming the norm and a requirement for SMEs to operate on business. By implementing a sustainability network within a real commitment towards improved performance, benefits to bottom line will result, improving the efficiency of operations, communication and interaction with stakeholders, and reduced negative effects on society and the environment. Existing tools and strategies that assist in the implementation of ISO 14001 still remain fragmented, trying to solve the ailmentsof all SMEs (Burke, 2007).
Many operations management tools, for example total quality management, ISO 9000 standards, excellence models and common assessment framework, reengineering, six sigma, lean systems, which are based on business process management techniques, increase structuring of organizational processes. Over-standardization of organizational processes is a reduced ability of organizational process members to adjust their behavior according to changes in the environment because of formally and informally imposed rules. Accumulation of rules and standards happens due to repetition, imposition and adoption of “structure-intensive” social and physical technologies (Wilkas, 2011).
Conclusion
Realized research brought interesting results, supporting the legitimacy of implementation ISO 9000 and 14000 in order to improve company’s performance. Hypotheses confirmed expected results, however seen from new perspective. Both ISO systems help to improve enterprise performance, however adopting ISO 14000 is rather a second step after implementation of ISO 9000; most enterprises with ISO 14000 adopted earlier ISO 9000 standard.
It is possible to find in literature some quality and environmental systems ex-post evaluation studies, which merely consider these systems as generally beneficial, however likewise burdened by some imperfections. ISO 9000 seems to be more widely accepted and tuned-up system than younger ISO 14000.
Acknowledgement
This paper was published and described research was realized with the support of students´ grant system by Silesian University in Opava, grant number SGS/9/2012.
References
Barnes, F. (2000). “Good Business Sense Is the Key to Confronting ISO 9000,” Review of Business.
Publisher – Google Scholar
Burke, S. & Gaughran, W. F. (2006). “Intelligent Environmental Management for SMEs in Manufacturing,” Robotics and Computer-Integrated Manufacturing, Nr. 22, pp. 566-575, Elsevier.
Publisher – Google Scholar
Burke, S. & Gaughran, W. F. (2007). “Developing a Framework for Sustainability Management an Engineering SMEs,”Robotics and Computer-Integrated Manufacturing, Nr. 23, pp. 696-703, Elsevier.
Publisher – Google Scholar
Gupta, S. & Kumar, V. (2012). “Sustainability as Corporate Culture of Brand for Superior Performance,” Journal of World Business, (in press), Elsevier.
Publisher – Google Scholar
Hillary, R. (2004). “Environmental Management Systems and the Smaller Enterprise,” Journal of Cleaner Production, Nr. 12, pp. 561-569, Elsevier.
Publisher – Google Scholar
Ilomäki, M. & Melanen, M. (2001). “Waste Minimization in Small and Medium-Sized Enterprises — Do Environmental Management Systems Help?,” Journal of Cleaner Production, Nr. 9, pp. 209-217, Elsevier.
Publisher – Google Scholar
Iraldo, F., Testa, F. & Frey, M. (2009). “Is an Environmental Management System Able to Influence Environmental and Competitive Performance? The Cease of the Eco-Management and Audit Scheme (EMAS) in European Union,” Journal of Cleaner Production, Nr. 17, pp. 1444-1452, Elsevier.
Publisher – Google Scholar
ISO (2009). ‘Environmental Management. The ISO 14000 Family of International Standards,’ [online],http://www.iso.org/iso/home/standards/management-standards/iso_9000.htm
ISO (2009). Selection and Use of the ISO 9000 Family of Standards, [online],http://www.iso.org/iso/home/standards/management-standards/iso14000.htm
Publisher
Kaynak, H. (2003). “The Relationship between Total Quality Management Practices and their Effects on Firm Performance,” Journal of Operations Management, Nr. 21, pp. 405-435, Elsevier.
Publisher – Google Scholar
Kočišová, K. & Tartaľová, A. (2010). ‘Podnikateľské Prostredie a Podnikateľský Index Malých a Stredných Podnikov na Slovensku,’ Acta Academica Karviniensia, Karviná.
Koc, T. (2007). “The Impact of ISO 9000 Quality Management Systems on Manufacturing,” Journal of Materials Processing Technology, Nr. 186, pp. 207-213, Elsevier.
Publisher – Google Scholar
Kovaľová, M. (2011). ‘Vybrané Problémy Implementácie Systému Riadenia Strategickej a Operatívnej Výkonnosti Podnikových Procesov,’ Acta Academica Karviniensia, Karviná.
Lundström, A., Almerud, M. & Stevenson, L. (2008). ‘Entrepreneurship and Innovation Policies — Analyzing Policy Measures in European Countries,’ IPREG.
MacDonald, J. P. (2005). “Strategic Sustainable Development Using the ISO 14001 Standard,” Journal of Cleaner Production, Nr. 13, pp. 631-643, Elsevier.
Publisher – Google Scholar
Mizla, M. & Pudło, P. (2012). “Å truktúra Nákladov Kvality a CitlivosÅ¥ Podnikov na Výkyvy Ekonomiky,” E+M Economics and Management, Liberec.
Publisher
Němeček, J., ÄŒebišová, K. & Hribik, J. (2011). ‘Comparing Economic Indicators of Companies in Dependence on Using Advanced Technologies,’ Hradec economic days 2011 — conference paper collection, Hradec Králové
Nenadál, J. & Noskievičová, D. (2005). “Moderní Systémy Řízení Jakosti — Quality Management,” Management Press, Praha.
Publisher
Pawliczek, A. (2011). “Udržitelný Rozvoj — Vybrané Aspekty z Oblasti Podnikání,” OPF SU Karviná.
Publisher
Pawliczek, A. & Piszczur, R. (2011). ‘Význam Strategického Řízení pro Stabilizaci Podniku v Kontextu Udržitelného Rozvoje, Ekonomika a Právo – Synergie Nebo Antagonizmus?,’ 6th annual international conference; Periodica Academica VÅ KE, Brno.
Pawliczek, A., Rylková, Z., Å ebestová, J., Antonová, B., Piszczur, R. & Veselá, K. (2011). ‘Adaptabilita Podnikání v Reakci na Turbulentní Politicko-Ekonomické Prostředí a Technologický Pokrok v Kontextu Udržitelného Rozvoje,’ (research report), OPF SU Karvina.
Google Scholar
Samson, D. & Terziovski, M. (1999). “The Relationship between Total Quality Management Practices and Operational Performance,” Journal of Operations Management, Nr. 17, pp. 393-409, Elsevier.
Publisher – Google Scholar – British Library Direct
Scott, J. T. (2010). ‘The Sustainable Business,’ First Edition, European Foundation for Management Development (EFMD), Brussels.
Å ebestová, J. (2012). ‘Strategy and Sustainable Business Development: Dynamic Hazard or Dynamic Mania? Lessons Learned from a Crisis,’ 2nd International Conference on Leadership, Technology and Innovation Management, Procedia Social and Behavioral Sciences,(in press), Istanbul.
Sharma, D. S. (2005). “The Association between ISO 9000 Certification and Financial Performance,” The International Journal of Accounting, Nr. 40, pp. 151-172, Elsevier.
Publisher – Google Scholar
Wade, J. (2002). “Is ISO 9000 Really a Standard?,” ISO Management Systems, [online], www.iso.org.
Publisher – Google Scholar
Wilkas, M. (2011). ‘Over-Standardization of Organizational Processes,’ The Journal of Economics and Management, Nr. 16, pp. 992-999, Kaunas.
Zakrzewska-Bielawska, A. (2011). ‘Wyzwania Rozwojowe Małych i Średnich Przedsiębiorstw — Innowacje,’ Technologie, kryzys, Difin, Warszawa.
Zorpas, A. (2010). “Environmental Management System as Sustainable Tools in the Way of Life for the SMEs and VSMEs” Bioresource Technology, Nr. 101, pp. 1544-15757, Elsevier.
Publisher – Google Scholar